How to Optimize MRO Inventory for Supply Chain Efficiency and Savings? 25 Jul 2024
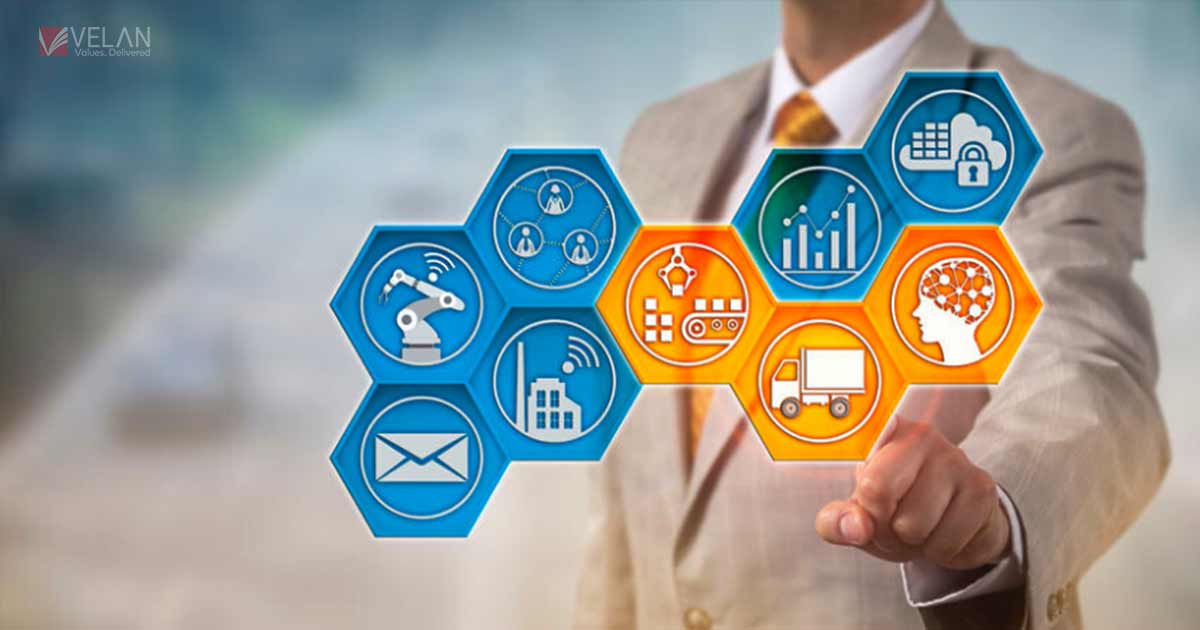
MRO teams are on the front lines in terms of many key problems associated with the aftermarket supply chain—risks like enhancing service levels, preserving working capital, retrieving spare parts, and avoiding downtime. However, very fundamental challenges, such as inventory management, can limit productivity in MRO.
According to a recent survey, inventory tracking is the second most common issue with spare parts inventories, followed by downtime. Accurate organization and monitoring of MRO inventory is necessary to minimize waste, misplacements, and losses.
We often underestimate the significant advantages that properly managing MRO inventory can provide over production inventory. Effective management of consumables can prevent unaccounted-for or idle MRO inventory, as well as stockouts.
Inventory optimization presents challenges for MRO and after-sales.
Here are some common challenges that MRO organizations, warehouse managers, and teams encounter when managing MRO inventory.
- Manage the scattered and large vendor networks
Consolidating the network of suppliers to meet the unplanned or reactive demand for the various consumables might be difficult if strategic vendor relationships are not developed.
- Segmenting inventory
MRO inventory is difficult to classify because it is consumable and secondary to production stock. Consequently, tracking and monitoring them becomes a problem.
Handling high inventory levels
Higher levels of safety stock result in higher holding costs and increased inventory susceptibility to obsolescence.
Managing outmoded inventories
There is practically no way of knowing if the merchandise has become obsolete since you have it in some far-off storage facility where no one can see it. Your MRO optimization strategy cannot afford to ignore these factors. However, those ongoing savings do incur a penalty.
Predicting demand and supply
The need for maintenance and repair is erratic and specific to tasks, making it difficult to forecast demand. These situations make supply delivery that much more time-sensitive and can result in a loss of hours.
Problems and Solutions: Excess slow-moving units due to overallocation of inventory for off-the-shelf components (or) increased savings in low-demand, slow-to-turn items.
Tips to Improve MRO Inventory Management
- Use the ABC categorization.
Create a universal classification structure to facilitate the partitioning of all critical consumables. This could potentially aid in the tracking of these entities. Categorizing low-value (already written off) but high-volume parts can help companies track waste and losses.
- Set and monitor KPIs.
Create key performance indicators (KPIs) to measure the performance of your inventory management system. These will show you whether or not the savings are worth the trouble.
- Maintain EBOM
Properly maintaining the BOM (bill of materials) for equipment helps during data entry by comparing the bill materials and actuarial materials. This, of course, helps you keep track of waste, misplacement, and theft. When a new part replaces an old one, you update the EVOM.
You should also know when to retire old parts and update your records on those that can no longer be reused. It’s important to submit formal requests, even for minor items that are on display.
- Outsource and manage MRO services.
Third-Party Fulfillment Streamlining Inventory Control Skillful managed services and consulting for MRO inventory management allow you to focus on what you do best. Professional engagement will ensure cleaner tracking of MRO consumables.
- Other MRO Inventory Management
Properly storing all the separated components and additional accessories is of significant importance to ensure a satisfactory track record of express delivery. The obvious limitation of doing them manually walking sequences (ironically using or stocking orbs—mistakes will happen; they need to be accounted for.) Blockers: label which ones are unique and stack them based on their designation.
- Identify important components.
Determine the things you need instantly through the important stuff and assure them that they are there. Downtimes are suffering for any business with a chance of high-value repair item unavailability. As a result, warehouse managers must be cautious when stocking such items and regularly monitor their usage.
Improved inter-departmental communication and operational
All companies transfer material regularly from branch to branch. Nonetheless, to ensure that there is no potential loss from theft or mishandling, the transportation of your products needs a clear invoice. It could have been introducing Kanban cards or its equivalent inventory movement system.
- Sophisticated ERP system
A system that integrates ERP with scientific inventory models helps to save time and costs by tracking timely replenishment and potential shortages.
- Manage the “hidden” inventory
Hidden inventory can be defined as stock that is difficult to find, such as in toolboxes, on shelves, or in closets. As a result, a suitable storage strategy is implemented for proper serving. In this case, instead of being scattered about in a thousand unknown spaces, it is better to have them centralized.
- Train the MRO teams.
We encourage training their MRO team members on classic inventory management techniques as part of the course.
- Utilize MRO analytical tools.
They use data management and demand forecasting tools, which are known as analytical tools for the MRO part. Because they have virtually no regular demand, analytics are an excellent way to detect pricing differences, duplicate records, and compare metrics—to save money. Analytical tools can discover new information that traditional record management systems might miss.
A disciplined MRO inventory strategy that utilizes domain expertise, flexible pricing models, and predictive analytics can be an invaluable ally in enhancing the efficiency of a firm’s supply chain.
MRO leaders need to seek out opportunities within inventory optimization that will translate into more help for the business. Teams: With the right skill sets, optimizing MRO inventory is not a task they will want to do.