How does inventory management operate and what does it implies? 14 Dec 2022
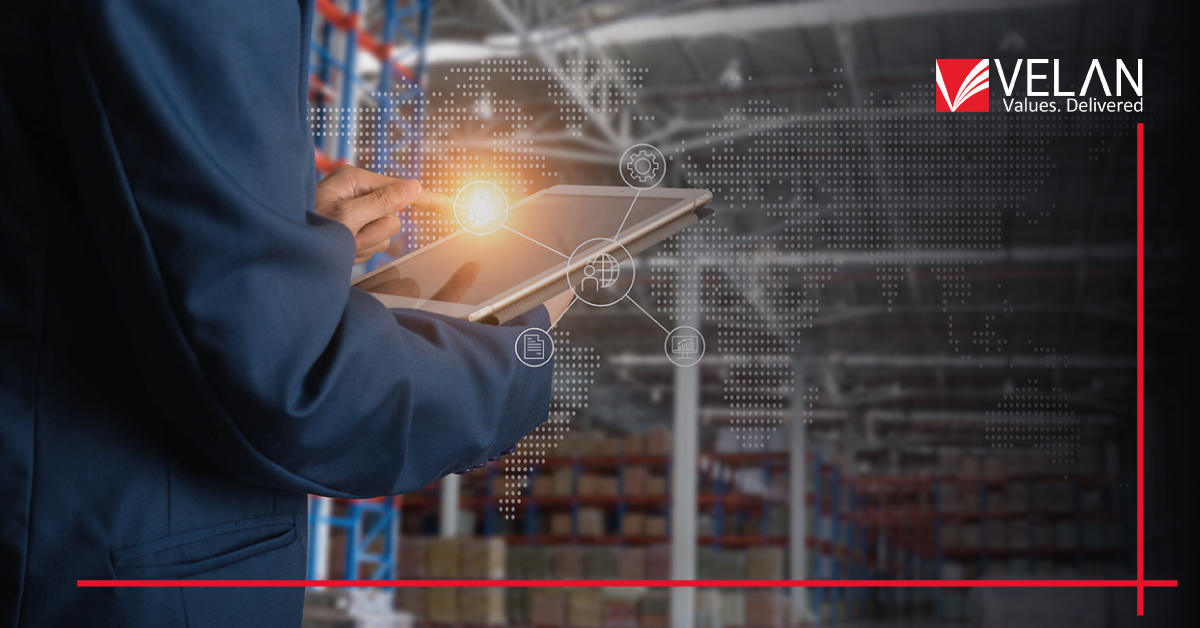
Understanding what you have, where it is kept, and how much you will need is the key to effective inventory management. But it’s easier said than done. Where Velan adds value is in this. Businesses utilize the Outsource Inventory Management System to lessen the burden of manufacturing the components of completed goods in-house, i.e., within the company. Thus, an Outsourcing Inventory management process is one that purchases items or parts from outside suppliers rather than manufacturing them in-house.
In order to support today’s interconnected, global corporate operations, Velan employs a multi-echelon approach to inventory management techniques. This strategy helps to reduce stock-outs and boost supply efficiency. The Inventory management software automates manual activities such as inventory traceability, replenishment, cycle counting, and inventory management across many sites.
- Velan helps clients manage their inventory using best-in-class procedures and very effective solutions.
- Velan has more than a dozen years of expertise managing inventory for hundreds of market-leading businesses worldwide.
- Offshore Inventory Management services to shipping companies such as Ship Owners, Ship Managers, Shipyards, and Offshore Vessels Support Vessels with the delivery of food, bonds, deck, and cabin goods.
What is the visibility of the inventory?
Inventory for multichannel order fulfillment operations is frequently dispersed across the supply chain. Knowing what inventory, you have and where it is situated is known as inventory visibility.
To ensure that client orders are fulfilled, shorten shipping turnaround times, and decrease stockouts, oversells, and markdowns, businesses require an accurate view of their inventory.
Why is inventory management crucial?
The most valuable asset of a business may be its inventory. Where all the components of the supply chain come together is inventory management. When there is insufficient inventory, customers may get dissatisfied. But a sizable inventory comes with its own risks, including the cost of storing and insuring it as well as the possibility of spoiling, theft, and damage. Businesses with intricate production and supply networks must strike the correct balance between having too much inventory on hand and not enough.
Planning the purchase, storage, and sale of stock—whether it be raw materials, components, or completed goods—to guarantee the proper kind and quantity of stock are accessible without keeping too much stock and tying up cash is known as inventory management. Inventory management may help businesses save money when done properly.
Why inventory is important in supply chain management?
Inventory management is a critical component of supply chain management that is sometimes disregarded.
Why inventory management is important in the supply chain? Inventory management experience is one of a prospective supply chain manager’s basic abilities.
- There’s a compelling reason why businesses should look for a supply chain manager with strong inventory management skills: Poor inventory management can have ramifications throughout the firm and have a negative impact on its bottom line.
- Too much inventory can also be a major inventory management issue. Overordering consumes cash, complicates warehouse management, and may result in a loss owing to an old or expired product that the firm is unable to utilize or sell.
- By maintaining a consistent inventory flow, efficient inventory management may raise profitability, improve supply chain visibility, and improve operations. For today’s supply chain management, inventory optimization is the gold standard.
The Operation of Inventory Management:
Understanding inventory levels and where it is located in warehouses is the aim of inventory management. The movement of goods from the supplier through the manufacturing process and to the consumer is tracked by inventory management software. Inventory management at the warehouse keeps track of stock receiving, picking, packaging, and shipment.
Terminology and Techniques for Inventory Management
Formulas and analysis are used in several inventory management strategies to plan stock. Others depend on protocols. Every technique aims to increase precision. A company’s methods are determined by its requirements and inventory. Here’s a summary of them:
- ABC Analysis
This method works by identifying the most and least popular types of stock.
- Bulk Shipments
This method considers unpacked materials that suppliers load directly into ships or trucks. It involves buying, storing, and shipping inventory in bulk.
- Consignment
When practicing consignment inventory management, your business won’t pay its supplier until a given product is sold. That supplier also retains ownership of the inventory until your company sells it.
- Cross-Docking
Using this method, you’ll unload items directly from a supplier truck to the delivery truck. Warehousing is essentially eliminated.
- Demand Forecasting
This form of predictive analytics helps predict customer demand.
- Dropshipping
In the practice of dropshipping, the supplier ships items directly from its warehouse to the customer.
- Economic Order Quantity (EOQ)
This formula shows exactly how much inventory a company should order to reduce holding and other costs.
- FIFO and LIFO
First in, first out (FIFO) means you move the oldest stock first. Last in, first out (LIFO) considers that prices always rise, so the most recently-purchased inventory is the most expensive and thus sold first.
- Just-In-Time Inventory (JIT)
Companies use this method in an effort to maintain the lowest stock levels possible before a refill.
- Lean Manufacturing
This methodology focuses on removing waste or any item that does not provide value to the customer from the manufacturing system.
- Materials Requirements Planning (MRP)
This system handles planning, scheduling, and inventory control for manufacturing.
- Minimum Order Quantity
A company that relies on minimum order quantity will order minimum amounts of inventory from wholesalers in each order to keep costs low.
- Reorder Point Formula:
Businesses use this formula to find the minimum amount of stock they should have before reordering, then manage their inventory accordingly.
- Perpetual Inventory Management
This technique entails recording stock sales and usage in real time.
- Safety Stock
An inventory management ethos that prioritizes safety stock will ensure there’s always extra stock set aside in case the company can’t replenish those items.
- Six Sigma
This is a data-based method for removing waste from businesses as it relates to inventory.
- Lean Six Sigma
This method combines lean management and Six Sigma practices to remove waste and raise efficiency.
What Is Inventory Management’s Primary Goal?
Making ensuring there are enough products or resources on hand to satisfy demand without overproducing inventory is the main goal of inventory management. Because it helps to ensure that there is rarely too much or too little product on hand, inventory management is essential to a company’s health because it lowers the danger of stockouts and erroneous records.
In order to comply with Securities and Exchange Commission (SEC) standards and the Sarbanes-Oxley (SOX) Act, public corporations must keep track of their inventory. To demonstrate compliance, businesses must document their management procedures.
What Benefits Does Inventory Management Offer?
Running a successful goods business depends on precise inventory management. Regular stock tracking can assist prevent stock mistakes and other issues. The advantages of effective inventory management include the following:
-
Better Inventory Accuracy:
With effective goods control, you are aware of what is in stock and only order the quantity of inventory required to satisfy demand.
-
Reduced Risk of Overselling:
Keeping track of what is in stock and what is back-ordered helps you avoid overselling items.
-
Savings:
Until it is sold, stock costs money. Carrying expenses include labor wages, storage, handling, and transportation costs. Inventory can also be lost due to theft, calamities, or obsolescence.
-
Avoiding Stockouts and Excess Stock:
A company may reduce the number of days an item is out of stock if any, and prevent holding too much inventory by better planning and management.
-
Greater Insights:
Inventory management and stock control make it simple to identify sales patterns, keep track of recalled goods, and monitor expiration dates.
-
Improved Relationships with Vendors and Suppliers:
Inventory management also reveals which items sell well and in what quantities. Utilize that information as leverage to bargain with suppliers for better rates and conditions.
-
More Productivity:
A time that could be spent on other tasks is saved by effective inventory management systems.
-
Profits Rise:
Increased inventory turnover results in higher profits since availability and demand are better understood.
-
A More Organized Warehouse:
A more organized warehouse minimizes labor costs and expedites order fulfillment by organizing its inventory according to demand, which goods are frequently sold together, and other variables.
-
Better Customer Experience:
Loyal customers are those who receive their orders promptly.
Velan Inventory Management services include:
Our experts help you plan your inventory better so that you have the right inventory, at the right time, and at the right location. Velan, help you optimize and manage all the components of your inventory operations, including cycle stock, safety stock, pipeline, and pre-build inventory to drive more efficiency across the value chain. Our services include:
-
Inventory Planning
The process of choosing the right amount and time of inventory with the goal of coordinating it with sales and production capacity is known as inventory planning. Planning an organization’s inventory has an impact on its cash flow and earnings and helps to ensure a smooth supply chain.
Which areas of an organization’s inventory planning process require improvement the most will determine the best course of action for improvement and maintenance? Businesses should evaluate their inventory management procedure to identify any flaws ex. maintaining too much stock in a warehouse.
- Utilizing a demand forecasting formula
- Performing regular stock counts
- Implementing software to automate manual processes
- Proper training and accountabilities.
-
Replenishment Services
Replenishment is the planned and regular transfer of inventory from a supply chain node upstream to one downstream that needs enough stock to meet demand. Depending on the type of business and the situation, the method of inventory replenishment varies. It may apply to any of the following circumstances, for illustrative example:
- Transporting raw materials from producers to production sites
- Transferring stock from places for packaging and shipping to the storage of reserve products
- Moving goods from a warehouse to a pickup location or retail, as well as ordering inventory from suppliers to make sure a warehouse or fulfillment center has enough merchandise.
-
MRO Inventory Planning
Maintenance, repair, and operation inventory are referred to as MRO inventory. All the consumable supplies, tools, and equipment required for manufacturing that isn’t included in the finished goods inventory are referred to as MRO inventory.
MRO Inventory Management: What Is It? The short answer is, yes. Longer response: MRO inventory replenishment is optimized through controls and procedures. What is referred to as “conventional inventory” typically requires the use of standard inventory management capabilities.
Inventory of raw materials, work-in-progress, manufactured goods, products, etc. Modern costing analysis and demand forecasting are applied to each of these inventory kinds. MRO inventory, however, isn’t normal. Measuring MRO inventory consumption or on-hand stock is uncommon. So it isn’t often optimized.
What kinds of inventory management are there?
-
Periodic inventory management
The periodic inventory system is a technique for valuing inventory for financial reporting needs that involves physically counting the inventory at predetermined times. With this accounting technique, the cost of goods sold (COGS) is. is calculated by taking an inventory at the beginning of a period, adding new inventory purchases during the period, and subtracting ending inventory.
-
Inventory management with barcodes
Businesses assign a number to each item they sell using barcode inventory management systems. The supplier, the size and weight of the item, as well as changeable information like the quantity in stock, may all be linked to the number.
-
RFID inventory control
Radiofrequency identification, sometimes known as RFID, is a technology that wirelessly broadcasts a product’s identity in the form of a distinct serial number in order to monitor things and offer comprehensive product information. The RFID-based warehouse management system may boost productivity, increase inventory visibility, and assure quick delivery and receipt recording.
-
Streamlining the Inventory Lifecycle
In order to increase efficiency throughout the value chain, Velan’s professionals assist you in optimizing and managing all the elements of your inventory operations, including cycle stock, safety stock, pipeline, and pre-build inventory.
With a number of tried-and-true inventory management strategies, Velan gives your business the agility it needs to quickly adjust to changes in demand without sacrificing the quality of its services. Our professionals assist you in enhancing supply efficiency and customer service standards by utilizing time-phased demand signals and Just in Time (JIT) solutions. To Read More Benefits of Supply Chain Management Outsourcing.